Jean-Pierre Fréry a capo di un equipaggio di 3 persone sta per iniziare un giro del mondo senza sosta intorno al mondo con i 3 mantelli su un catamarano di produzione ( vedi la nostra presentazione del progetto Cavok ). Per questo motivo ha acquistato una Lagoon 400 S2 che gli è stata appena consegnata a Saint-Gilles-Croix-de-Vie. Questo n°544 della serie è uno degli ultimi esemplari costruiti. Il cantiere Lagoon ha infatti varato un nuovo Lagoon 40 al salone nautico di Cannes nel settembre 2017 per sostituirlo.
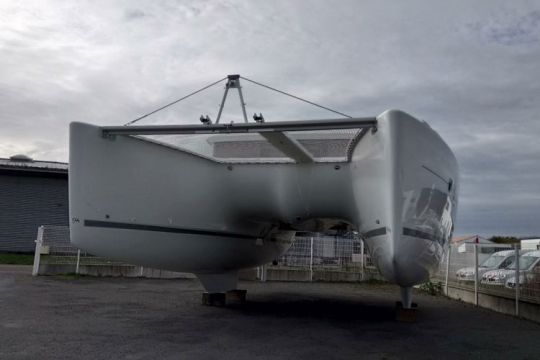
Cavok (è il nome della Laguna 400 S2) non è stato costruito come prototipo, ma come barca a vela di produzione. Tutti i soliti servizi di questo tipo di catamarano saranno a bordo. Solo alcune raccomandazioni sono state richieste al sito per ottimizzare l'affidabilità e la sicurezza di Cavok.

Infatti, cinque mesi in mare, metà dei quali in acque particolarmente inospitali, richiedono alcune precauzioni, soprattutto per quanto riguarda l'impermeabilizzazione. Le modifiche più visibili sono l'assenza di un oblò per l'illuminazione delle cabine. Questi non sono stati tagliati dallo scafo per evitare di indebolirlo. Si noti inoltre che le pareti divisorie a tenuta stagna sono installate nella parte anteriore e posteriore, che non esistono in serie. Per il resto, la costruzione è di serie con una sola cura per l'incollaggio, alcuni rinforzi nei punti di fissaggio come le pulegge o i tacchetti (che verranno utilizzati per appendere le cinghie per rallentare la barca in mare mosso).
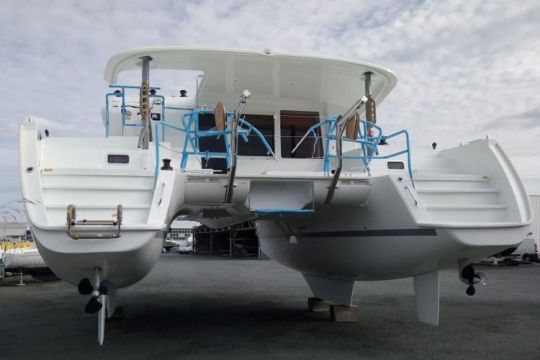
Altri accorgimenti sono più legati alle prestazioni, come la preparazione dello scafo con una piccola cipolla o l'installazione di un bompresso orientabile per facilitare l'installazione dello spinnaker sottovento.
In caso contrario, il Lagoon 400 S2 è rigorosamente standard. L'albero, ad esempio, è il modello standard, i mantelli e le piastre catena non sono rinforzati...
Ecco l'elenco completo del lavoro svolto a bordo per questa speciale "crociera":
Impermeabilità :
- Schiuma di tubi in PVC paratie anteriori e posteriori
- Sbavatura di taratura e doppio cordone di colla durante il montaggio dei pannelli di sopravvivenza
- Montaggio di boccaporti da 50 mm dotati di soffietto per il passaggio delle linee a barre nella parete posteriore
- Installazione di pareti divisorie e moduli nello scafo: incollaggio completo compresa la parte superiore
- Particolare cura nell'assemblaggio di elementi come l'elettronica per mantenere una perfetta tenuta stagna delle pareti posteriori
Sicurezza :
- I condotti dello scafo vicino alla linea di galleggiamento (prese d'acqua nera, lavandino) saranno dotati di una valvola.
- Bitte posteriori rinforzate con una grande contropiastra per l'uso con i ritardatari. Se non sono accessibili, infilare in una contropiastra in alluminio.
- Stivaggio dello scaldabagno mediante bullonatura o bulloni rinforzati.
- Stivaggio rinforzato dei serbatoi di carburante
- Stivaggio rinforzato di serbatoi di acqua dolce
- Installazione sopraelevata di due pompe di sentina
- Controllo specifico dell'albero e del sartiame in piedi da parte di Z-Spars
- Dadi in acciaio inox da montare su tutti i deflettori in acciaio inox
Parti soggette ad usura:
- Tutte le pulegge del sartiame sono in alluminio
Rinforzi :
- Ripresa della stratificazione del collegamento guscio/ponte con gli archi
- Ventilazione del motore laminato e piastra della botola BIB nella parte inferiore
- Ripresa della stratificazione dei tubi jaumière allo zafferano
- Nessuna perforazione nello scafo per finestre fisse (rimozione delle finestre in plexiglass)
- Rinforzo strutturale delle piastre sottobarre
- Contropiastra in alluminio di grandi dimensioni per tacchette, ancoraggi delle pulegge in lamiera gennaker e piastre portacatena anteriori
- Nuova base del montante adattata ad un cannotto più basso e più tollerante in caso di carico molto elevato (meno rigido)
Prestazioni :
- Nuova pedana per il bompresso, articolata su due assi per ottimizzare le prestazioni delle vele sottovento
- Preparazione dello scafo mediante carteggiatura del gelcoat e finitura liscia di chiglie e timoni.
- Smussatura dei bordi d'uscita per ridurre al minimo le vibrazioni
- Stratificazione della grondaia centrale
- Trattamento a filo dell'anodo di messa a terra
Autonomia :
- Installazione di un dissalatore nella cabina di prua del porto
- Batterie AGM