Alla fine del 2015, Bénéteau ha avviato uno studio per progettare una nuova barca. Le specifiche sono redatte dalla classe Figaro, che comprende tutti gli armatori e gli skipper. Insieme hanno definito la barca in termini di obiettivi di regata, costi - la barca non dovrebbe essere più costosa di una Figaro 2 o 150 000 ? - e peso. L'idea era quella di realizzare una barca più leggera con la stessa stabilità e senza zavorra - da qui l'uso di lamine. È stata inviata una gara d'appalto e sono stati selezionati 5 architetti. Due di loro hanno offerto barche equipaggiate con fogli di alluminio. Sono state studiate anche la chiglia basculante o le tavole di pugnali, ma sono state abbandonate per motivi di bilancio - un paio di fogli che costano già 30.000 euro.
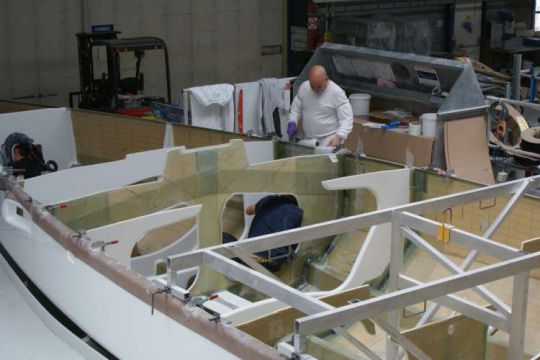
Visita del sito
Siamo andati a visitare il cantiere Bénéteau che produce queste nuove imbarcazioni. Questo sito, inaugurato nel 1992, ha costruito trimarani da corsa per il marchio Jeanneau. Dopo alcuni anni è stato riabilitato per il lancio di Figaro 3. Per un investimento di 3 milioni di euro, l'edificio è stato chiuso per creare un locale specifico per l'infusione dove la temperatura e l'idrometria sono controllate: 20°C e 50% di umidità.
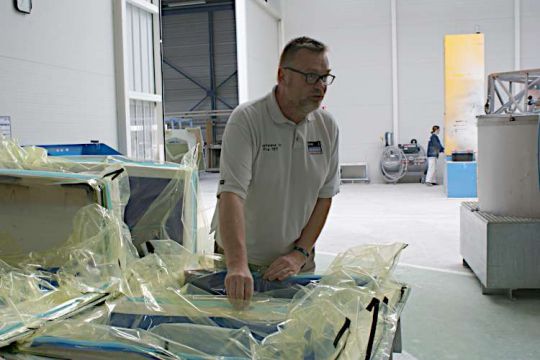
Competenze interne
All'interno di questa entità, Marc Vaillier - project manager - ha raccolto le migliori competenze: giovani motivati che ha formato per costruire una barca di alta gamma. È stato poi necessario anticipare la somma civettuola di 8 milioni di euro per poter costruire le prime 50 unità. All'ultimo Nautic 2018 a Parigi, gli armatori hanno estratto a sorteggio il loro numero di scafo. La prima persona che ha compilato il modulo d'ordine è stata la prima ad estrarre il numero di barca e ad essere consegnata dopo il salone nautico. Le prime 50 barche sono state consegnate in 3 settimane.
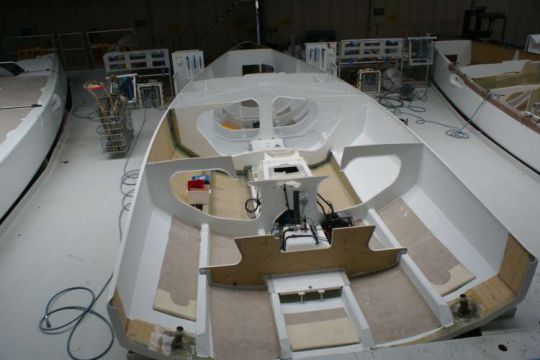
Una Figaro 3 ogni 4 giorni
L'officina situata sotto il ponte Cheviré a Nantes è in grado di produrre un Figaro Bénéteau 3 in 20 giorni. Una barca lascia la fabbrica ogni 4 giorni. Per tenere il passo con questo ritmo, sono necessari molti strumenti perfettamente calibrati. Ad oggi, 70 Figaro 3s hanno lasciato la fabbrica e il singolo stampo dovrebbe essere in grado di produrre circa un centinaio.
Rigore e precisione sono essenziali per poter rispettare un rigoroso one-design. Un drastico controllo di qualità viene attuato dal sito. La quantità di materiale viene attentamente monitorata e ogni pezzo viene pesato all'uscita dello stampo. La differenza di peso tra gli scafi più pesanti e quelli più leggeri è di soli 18 kg - su uno scafo finito di 2920 kg. Questa differenza di peso è compensata da scrofe distribuite tra la parte anteriore e posteriore.
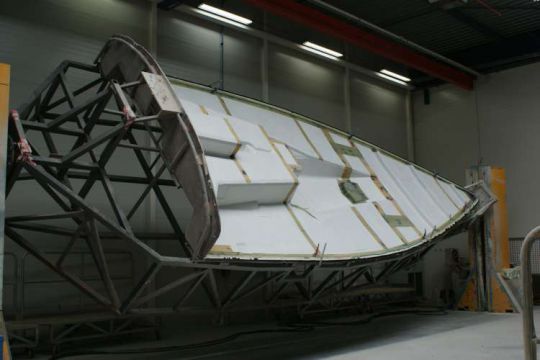
Differenze minime tra gli scafi
I primi 22 scafi sono stati scansionati digitalmente dal loro proprietario. È stato possibile misurare una deviazione di soli tre decimi. Ad esempio, sulla chiglia "peggiore" è stato trovato un offset di 0,12 gradi a dritta. La posizione della lamina peggiore e 5/10 di millimetro a dritta. Ogni foglio pesa 36,5 kg e c'è una differenza di 420 g tra il più pesante e il più leggero. La punta del foglio, una volta uscito dal pozzo, rientra in uno spazio inferiore a 10 mm per le 60 barche. Nella maggior parte dei casi la precisione di montaggio è inferiore alla precisione di misura.
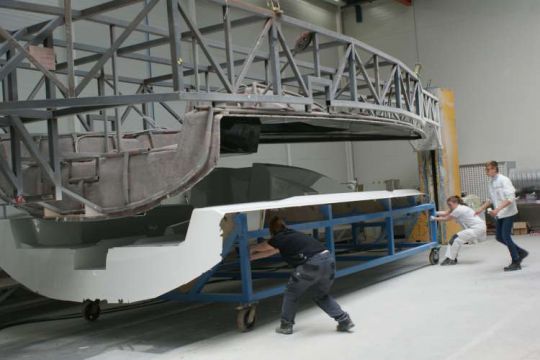
Modelli per la posa dei tessuti
Il guscio è fatto per infusione. Per un guscio completo, sono necessari 576 pezzi di tessuto in fibra di vetro. Ogni pezzo viene tagliato digitalmente internamente e posizionato utilizzando un modello in modo che ogni sovrapposizione sia identica su tutte le imbarcazioni. Per ottenere questo risultato, il manuale tecnico di costruzione ha una lunghezza di oltre 200 pagine.
Per ottimizzare il peso nel rispetto delle norme ISO, sono stati progettati tessuti specifici in collaborazione con architetti e produttori per ottenere un peso ottimizzato. Un tessuto diffusore - che aiuta la migrazione della resina in zone dove c'è molto spessore - è stato sviluppato appositamente per questo progetto. Dietro la chiglia o le lamine, ci sono fino a 65 spessori di tessuto. Senza questo specifico tessuto diffusore, ci sarebbe il rischio di rimanere zone asciutte nel cuore del composito.
La struttura della chiglia e la struttura longitudinale sono infuse contemporaneamente allo scafo. Gli elementi di fissaggio dei bulloni della chiglia sono inclusi nello stampo. Non è necessaria alcuna perforazione attraverso il guscio.
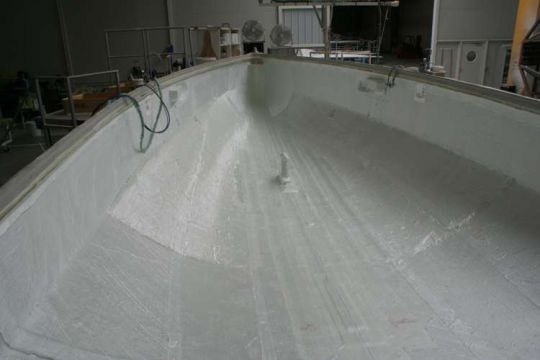
4 giorni su 4 postazioni di montaggio
La linea di montaggio è composta da 4 stazioni in cui ogni barca trascorrerà 4 giorni. Sulla prima delle 4 stazioni, le pareti divisorie sono posizionate con sagome e incollate con colla metacrilato. Le 3 partizioni principali hanno anche un ulteriore strato di recupero. Lo scafo viene spostato nella posizione successiva dopo 4 giorni lavorativi. E' posizionato grazie all'albero della chiglia in modo che gli utensili di ogni stazione siano perfettamente allineati.
Nell'ultima stazione, lo scafo è chiuso dal ponte, che è già preacceso.
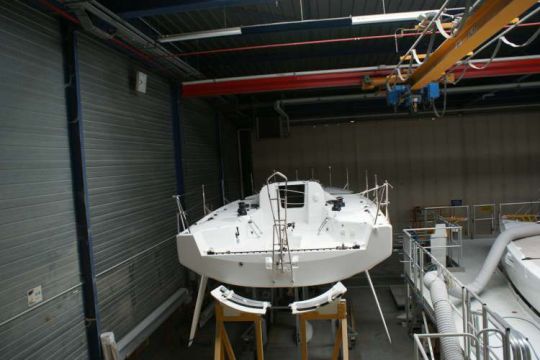
Nessun carbonio in questo laboratorio
Poiché l'officina non è attrezzata per lavorare con resina epossidica e carbonio (per motivi legislativi), in questa officina non vengono prodotte solo 3 parti: le lamine - prodotte da Multiplast - il bompresso e i timoni - prodotte in un'officina collettiva in Polonia.
Grazie a tutte queste misure, il cantiere assicura un rigoroso one-design delle barche. Se è necessario apportare una modifica ad uno di essi, essa dovrà essere applicata anche all'intera flotta. Oltre ai problemi di sartiame gestiti dal costruttore dell'albero, il sito è stato costretto, ad esempio, a rinforzare il supporto del cilindro pilota quando le prime 50 unità erano già state consegnate. Ma questo rigore permette agli skipper di liberarsi dai sospetti di disuguaglianza tra le barche e di concentrarsi sulla loro navigazione.